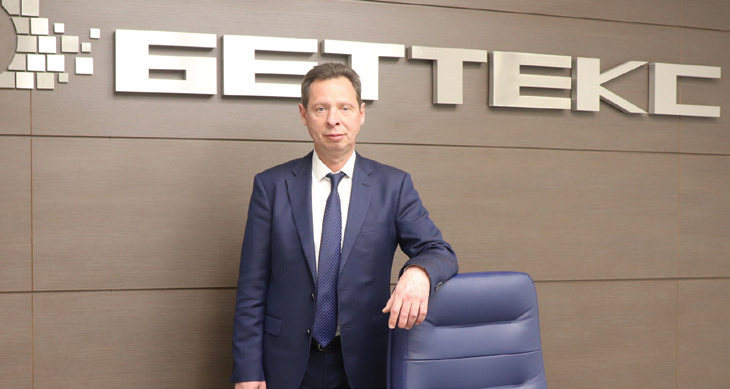
Сейчас в «АксайСтройПроме» завершается проект по повышению производительности труда, который реализуется при активном участии Регионального центра компетенций (РЦК), действующего при Агентстве инноваций Ростовской области. Эта работа уже позволила предприятию на основном участке на 50% снизить время протекания процесса и на 23% увеличить выработку в смену на одного работника. Об этом исполнительный директор компании Евгений Дудченко рассказал «Эксперту ЮГ».
Кризисы — лучшее время для улучшений
— Насколько сильно кризис 2020 года повлиял на привлекательность вашей работы по повышению производительности труда?
— Как, наверное, многие мои коллеги — руководители производственных компаний — считаю, что привлекательность такой работы только выросла. Кризис способствует тому, чтобы предприятие искало скрытые резервы снижения себестоимости выпускаемой продукции и всех условно-постоянных затрат. Работа такая должна быть системной. Если не реализовывать весь комплекс мер, направленных на повышение выработки на каждого работника, устранение потерь, борьбу с незавершённым производством, рискуешь потерять рынок, потребителей, бизнес.
— Вырос ли в 2020 году уровень инвестиций вашей компании в новые технологии повышения производительности?
— Весной, когда началась пандемия и был период неопределённости, мы приняли решение приостановить инвестпроекты. Перенесли их реализацию на 2021 год. Поэтому сейчас мы не вкладываем средства в новые технологии. Подчёркиваю, это — временная мера. Сегодня готовим инвестиционный бюджет на 2021 год. В наших планах, в частности, приобретение дополнительного оборудования и модернизация производственных линий. Это будет способствовать росту производительности труда и устранению потерь.
— Что сегодня в наибольшей степени мотивирует вас заниматься повышением производительности труда?
— С одной стороны, для меня главным мотиватором является повышение экономических показателей компании (выручки, прибыли). «АксайСтройПром» — коммерческое предприятие. Надо зарабатывать деньги, приносить собственнику прибыль. С другой стороны, не всё можно оценить в деньгах. Например, настроение коллектива, которое, благодаря улучшениям, меняется в лучшую сторону. Приятно видеть, как постепенно вся команда завода (а это почти 200 человек) включается в процесс улучшений, видеть, что это стало не только моей заботой, но и заботой буквально каждого специалиста. Люди начали тщательно следить за порядком на местах, за сохранностью оборудования и инструмента. Это дорогого стоит.
— Делаете ли вы замеры производительности труда на одного сотрудника?
— Конечно. У нас существует два критерия. Первый — количество произведённой продукции в натуральном выражении. За единицу измерения берётся объём, сделанный одним сотрудником за одну смену. Так, в 2019 году этот показатель составлял 1700 квадратных метров плитки и 1800 единиц штучных бетонных изделий. Второй критерий — чистый объём продаж на человека в год. В 2019 году это было 2,136 миллиона рублей. Такой подход к оценке производительности позволяет нам анализировать эффективность каждого работника как с точки зрения чистого производства, так и через призму продаж. Если мы видим, что физические объёмы конкретного продукта растут, а его реализация идёт слабо, то переключаем этого рабочего на выпуск продукции, пользующейся спросом.
Дефицит времени как вызов для директора
— Какова динамика производительности труда на предприятии за последние годы?
— Последние несколько лет на предприятии наблюдается рост производительности труда в среднем на 10 процентов в год. Например, в 2019-м, как я уже говорил, производительность труда на основном участке у нас превышала 1700 «квадратов» на человека. В 2020 году мы планировали увеличить эту цифру на 10 процентов. По итогам работы за 11 месяцев вижу, что задачу выполним.
— Каких ресурсов вам больше всего не хватает для работы по повышению производительности труда?
— Не буду оригинальным и скажу, что самый дефицитный ресурс — время. К сожалению, в сутках всего 24 часа. И их, поверьте, мало. Остальные ресурсы (деньги, кадры, знания) можно восполнить, а вот потерянное время — нельзя. Сделать так, чтобы времени хватало всегда и на всё — для меня вызов, с которым борюсь каждый день.
— Как вы оцениваете производительность труда на вашем предприятии по сравнению с показателями по отрасли в целом?
— Уровень производительности труда в ООО «АксайСтройПром» примерно такой же, как в среднем по отрасли. Но мы только в 2020 году стали серьёзно заниматься этим вопросом. Не скажу, что раньше такая работа у нас вообще не велась. Мы повышали производительность, внедряли некоторые бережливые инструменты, как могли, боролись с потерями. Но эта работа не была системной. Знаний и навыков, позволяющих такую систему создать и запустить, у нас не было. Мы принимали и внедряли точечные решения, касающиеся наиболее острых проблем производства (например, брака) и не видели картины в целом.
И только в уходящем году мы всё структурировали, описали, составили детальный план внедрения. Сейчас разрабатываются документы по применению инструментов бережливого производства, затем будет сформировано Положение о функционировании системы бережливого производства на предприятии. У него будет статус программного документа.
Сейчас у нас качественно иной подход к внедрению бережливых технологий, благодаря специалистам РЦК и лично руководителю проекта Игорю Колоскову. Партнёрство с центром, региональным Агентством инноваций позволило нам создать рабочую группу для внедрения лин-технологий, специалисты компании прошли обучение. Развитие системы бережливого производства начали с малого — выбрали один поток и стали проводить улучшения. Опыт, который мы сейчас нарабатываем, можно будет потом распространить и на другие производственные участки.
Делать больше, быстрее и лучше
— Какие задачи по повышению производительности вы ставите на ближайшие годы?
— В горизонте двух лет мы планируем внедрение на производстве системы 5S и повышение производительности труда минимум на 20 процентов. Это произойдёт за счёт снижения времени переналадки оборудования, сокращения брака и повышения эффективности внутризаводской логистики.
— Какие инструменты бережливого производства вы сейчас используете?
— Пока мы выбрали пять инструментов, применение которых принесёт компании наибольший эффект. Это система 5S (организация рабочего пространства), SMED (быстрая переналадка), TPM (система всеобщего обслуживания оборудования), расчёт эффективности использования оборудования (OEE) и система встроенного и всеобщего менеджмента качества (QA). В дальнейшем, возможно, нам понадобятся и другие инструменты из бережливого арсенала. Например, такие, как канбан, система JIT (от английского Just-In-Time — точно вовремя) и культура непрерывных улучшений.
— Какие препятствия для внедрения бережливого производства вы считаете главными?
— Главными для себя мы считаем два барьера. Первый — дефицит инвестиций в модернизацию. Выше я говорил, что мы были вынуждены заморозить нескольких проектов, что было логичным шагом в условиях кризиса и всеобщей экономической неопределённости. Если ситуация в стране и мире будет такой, как сейчас, или улучшится, то в следующем году разморозим проекты. Тогда смогу более детально говорить о них (размер вложений, окупаемость и т. д.).
Второй барьер — дефицит партнёров, способных обеспечить поставки необходимых нам сырья и материалов с учётом происходящих у нас улучшений. С поставщиками сейчас ведём переговоры. Думаю, уже в 2021 году мы сможем наладить поставки всего, что необходимо нам в изменившихся условиях.
— Как сейчас складываются ваши взаимоотношения с Агентством инноваций Ростовской области?
— К участию в национальном проекте «Производительность труда и поддержка занятости» мы подключились в июне 2020 года. Реализация проекта рассчитана на шесть месяцев, скоро будем подводить итоги. Для создания образцового потока мы выбрали участок по изготовлению тротуарной плитки, которая занимает в общих объёмах более 70 процентов. Ассортимент — широкий: 75 наименований, свыше 30 вариантов по цвету и 52 формы. Для изготовления плитки применяем современную технологию полусухого вибропрессирования на оборудовании немецкой фирмы HESS. Наше производство — одно из крупнейших на Юге. По объёмам изготовления тротуарной плитки уступаем только кубанской компании, которая выросла из местного производителя в федерального. У нас было желание сохранить рыночные позиции. А это возможно, в том числе, и через применение бережливых технологий.
Так вот, на старте проекта мы совместно с РЦК определили задачи, которые надо было решить: снижение на 50 процентов времени протекания процесса, сокращение на 36 процентов объёмов незавершённого производства и увеличение на 23 процента выработки в смену.
За первые три месяца команда РЦК провела анализ выбранного потока и выявила около 98 проблем, влияющих на производительность. Для исправления ситуации был применён производственный анализ всех этапов изготовления плитки, создана «Фабрика идей». При помощи специалистов центра мы запустили процесс оптимизации системы планирования производства (с упором на увеличение отгрузки готовой продукции). А главное, был составлен чёткий план на вторые три месяца.
Подведение окончательных итогов впереди. Но уже сейчас мы видим, что все поставленные задачи выполнены. Кроме того, в рамках проекта мы добились снижения на треть объёмов склада инертных материалов и на семь процентов увеличили производительность дробильно-сортировочного устройства. Мы надеемся, что и после завершения проекта будем находиться в активном контакте с командой РЦК.