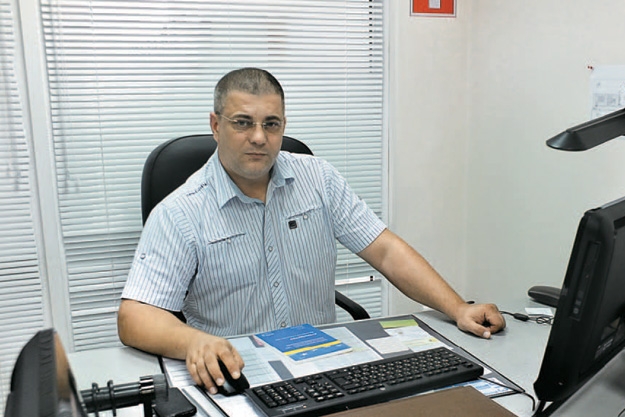
Поделиться
Технология с двойным действием
КДК является дочерней компанией УК «Сберинвест», специализирующейся на управлении венчурными фондами. Сумма инвестиций в проект «КДК-Холмская» составила 116 млн рублей. Основная часть средств была вложена закрытым паевым фондом УК «Сберинвест». Расчётный срок окупаемости проекта — около 4 лет. В дальнейшем для развития бизнеса планируется привлекать внешние инвестиции. Также в развитии проекта принимает участие фонд энергетической отрасли «Наноэнерго», созданный при участии «Роснано Капитал», дочерней компании ОАО «Роснано».На разработку технологии утилизации рисовой лузги у создателей проекта ушло около десяти лет. С начала сентября ведутся работы по возведению самого комплекса, в середине октября начнут устанавливать оборудование. Запустить комплекс планируется не позже января 2014 года. Строительство идёт в Холмском сельском поселении Абинского района Краснодарского края, где компания арендовала земельный участок в 6 тысяч кв.м. Надо отметить, что место выбрано не случайно — здесь сосредоточено порядка 90% всех рисовых угодий региона. «Краснодарский край является ключевым регионом России по выращиванию этой культуры, — поясняет руководитель информационно-аналитического агентства Cleandex Антон Липатов. — По оценкам “Роснано”, ежегодный объём отходов составляет около 180 тысяч тонн. Одно только решение вопроса утилизации этого объёма — уже веская причина для того, чтобы этот проект жил».
Участок, арендованный КДК, принадлежит крупному краснодарскому рисопроизводителю ООО «Южная рисовая компания» (входит в ГК «Агроальянс»). Такая непосредственная близость к перерабатывающему предприятию исключает все логистические издержки: именно Южная рисовая компания будет основным поставщиком рисовой шелухи. Перерабатывающие мощности производства КДК составляют полторы тонны в час, порядка 35 тонн лузги в сутки с получением зольного остатка в стартовом виде около 5–6 тонн в сутки.
«Технологический процесс достаточно прост: источник сырья — рисовая шелуха, при её окислении в котле-утилизаторе выгорают все органические вещества, кроме кремне‑ и углеродосодержащих элементов, — рассказывает генеральный директор КДК Александр Широких. — После основной операции происходит разделение технологии на два направления: первое — доработка зольного остатка, второе — использование генераторного газа для получения электроэнергии».
«Образующийся генераторный газ позволяет восстанавливать энергию отходов; его дальнейшая утилизации для электрогенерации — стандартная практика современных заводов по температурной утилизации отходов (мусоросжигательных, газификации, пиролиза)», — добавляет Антон Липатов. По сути, КДК будет выступать основным поставщиком энергии и тепловых мощностей для Южной рисовой компании. «Отходы переработки риса раньше приносили только головную боль в виде штрафов по экологии, при использовании нашей технологии лузга становятся главным источником энергии для предприятия-переработчика, — говорит Александр Широких. — В итоге необходимость потребления электроэнергии от сетевых источников у Южной рисовой компании сведется к нулю или резервному варианту». КДК сможет поставлять порядка одного мегаватта электроэнергии в час , в то время как средний часовой объем потребления электроэнергии у Южной рисовой компании в пиковые месяцы составляет до 900 кВт, в остальные 300–500 кВт. Таким образом, проект предполагает получение прибыли по двум направлениям: продажа тепловой энергии и производство диоксида кремния.
Полученное после всех технологических этапов вещество, чёрный порошок диоксида кремния, КДК планирует поставлять ведущему российскому производителю шин — компании «Кордиант». Использование диоксида кремния при производстве различных видов резин, в том числе шин — весьма распространённая за рубежом практика. «Например, производство аморфного диоксида кремния использует при изготовлении автомобильных покрышек мировой гигант Pirelli, — рассказывает г-н Липатов. — В 2015 году с этой технологией компания намерена выйти на новую проектную мощность в Бразилии, она будет обеспечивать около трети потребностей бразильских заводов компании в этом виде продукции».
Дальнейшая переработка полученного диоксида кремния в белый порошок позволяет использовать его в фармацевтике и химической промышленности. Однако на данном этапе для КДК приоритетным направлением стало всё же создание энергоэффективного производства с возможностями поставок тепловой энергии для своего непосредственного потребителя, Южной рисовой компании.
Нашлись конкуренты
Проект КДК будет первым действующим производством такого рода в России. Однако уже сегодня у компании есть потенциальные конкуренты. Технологию получения диоксида кремния из рисовой шелухи внедряет московский игрок — ООО «Рисилика», портфельная компания ООО «Фонд посевных инвестиций РВК» (ФПИ РВК). Разработкой проекта она занимается с конца 2011 года. «Рисилика» обладает собственной исследовательской площадкой в технополисе «Москва», где сейчас происходит наладка технологической линии. Проект находится на стадии проверки работоспособности продукта в имеющихся композициях и рецептурах. Технологическая мощность предприятия значительно меньше, чем заявленный объём переработки краснодарских игроков — порядка 1,5-2 тонн в месяц. Но речь идёт пока о пробных объёмах. В дальнейшем «Рисилика» планирует разместить свои основные производственные мощности или в Краснодарском, или в Приморском крае — в последнем сосредоточено порядка 10% от общего объёма посевных площадей риса в России. Пока ориентировочная мощность производственной площадки московской компании составит около 10–12 тысяч тонн в год. Запуск запланирован не раньше, чем на 2014 год.Главное отличие московского проекта в том, что при переработке рисовой шелухи диоксид кремния будет сразу получен в виде белого порошка. Такой продукт на порядок выше и по качеству, и по цене. «По предварительным договорённостям нам предлагают покупать рисовую шелуху по 150 рублей за тонну. С учётом того, что конечный продукт может стоить в районе 50–70 тысяч рублей за тонну, вы можете себе представить, насколько выгодным может быть такое производство», — поясняет управляющий партнёр ООО «Рисилика» Александр Комаров.
Впрочем, КДК и «Рисилика» вряд ли станут прямыми конкурентами. Несмотря на то, что компании предлагают довольно схожие проекты, задачи, которые они ставят перед собой, разные. Для краснодарской компании на первом плане получение генераторного газа и продажа тепловой энергии своему партнёру, для ООО «Рисилика» — производство самого диоксида кремния. К тому же по качеству продукта производители займут разные ниши. «Для нас приоритетным направлением является лакокрасочная промышленность, в частности, производство теплосберегающих красок. Нам также интересна резинотехническая промышленность, например, в качестве компонента шин. На Западе эти проекты пытаются осуществить под названием “зелёная шина”, — рассказывает г-н Комаров. — К тому же сегодня мы реализуем тестовые продажи порошка для клеевых материалов. А в ближайшее время компания планирует провести клинические исследования для использования нашего материала в фармацевтической и косметической промышленности».
Стоимость проекта «Рисилика» не раскрывает, однако подчёркивает, что срок окупаемости составит около 5 лет. «Одним из основных инвесторов, наряду с частными лицами, выступает Фонд посевных инвестиций РВК, — поясняют в компании. — В дальнейшем ООО “Рисилика” планирует выходить на второй раунд инвестирования. Мы надеемся, что один из венчурных фондов РВК тоже выразит желание сопровождать проект. Кроме того, в ближайшей перспективе мы планируем стать участником инновационного центра “Сколково”».
Тиражирование в условиях ноу-хау
Обе компании заявляют о безусловной необходимости развития данного метода утилизации. Однако, как отмечает Александр Комаров, реализовать технологию в условиях, близких к промышленным масштабам, в настоящее время так и не получилось ни у одной исследовательской группы, несмотря на то, что попытки развивать эту идею предпринимались ещё два столетия назад. «Первые патенты по данной тематике зафиксированы ещё в начале XIX века, однако реализованной в промышленности технологии до сих пор нет. На практическое подтверждение разработок пока решились лишь две компании. До сих пор даже европейские исследователи, столь избалованные инновациями, не смогли представить рабочих аналогов. Как объясняют эксперты, сложность такого проекта состоит в том, что он развивается на стыке сразу нескольких отраслей. Если для поддержания работы подобного комплекса требуется штат всего из пяти-шести человек, то для разработки технологии привлекаются целые научные объединения химиков, физиков-энергетиков, агробиологов. Однако ещё 10 лет назад такой острой необходимости в утилизации отвалов рисовой лузги не возникало.«Рынок энергетических установок по утилизации лузги ещё не разделён, и свои предложения выставляют фирмы из Индии, Южной Кореи, Германии. Некоторые зарубежные компании крайне заинтересованы в развитии данных технологического оборудования в России», — рассказывает Александр Широких. Но пока за технологиями закреплён статус «ноу-хау», ни одна компания не готова к сотрудничеству со сторонними игроками. «Нам пока сложно представить условия сотрудничества с зарубежными партнёрами, — поясняет Александр Комаров. — Мы хотим сохранить ноу-хау за нашей портфельной компанией. А если мы начнём проводить какую-то совместную работу с другими компаниями, то волей-неволей будем вынуждены раскрывать технологические секреты нашей разработки. Именно по этой причине мы отказались от предложения тиражировать наш опыт и заниматься поставками нашего оборудования. Только представьте — сегодня мы продадим оборудование, и завтра же на рынке появятся его копии от других производителей. Ни для кого не новость, что в рисовой шелухе высокое содержание кремния — вокруг этой сладкой идеи ходило много компаний. Однако все зарубежные концерны, которые пытались реализовать подобные проекты, потратили десятки миллионов евро, но так и не добились результата. Внедрить работающие технологии удалось только нам и нашим коллегам из Краснодара».