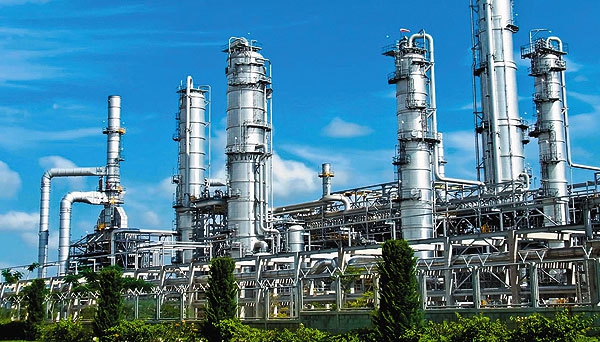
По данным Министерства энергетики РФ, в ближайшие три года нефтегазодобывающие операторы и переработчики углеводородов, работающие на юге России, большую часть оборудования и технологий для своей деятельности будут закупать у отечественных производителей. В министерстве надеются сократить импортозависимость в ТЭК к 2020 году с нынешних 60 до 43%. Объём российского рынка нефтегазового оборудования составляет порядка 5 млрд долларов ежегодно. В ЮФО уже сегодня ряд компаний могут предложить продукцию для отечественных вертикально интегрированных холдингов (ВИНК).
Трави помалу
Сегодня, по данным Минэнерго, на долю импорта пока ещё приходится 80% в программном обеспечении и катализаторах для НПЗ и нефтехимии, 50% в насосно-компрессорном оборудовании, 20% в сегменте пластинчатых теплообменников для нефтепереработки.
Главными направлениями для импортозамещения являются технологии гидроразрыва пласта (ГРП) и наклонно-направленного бурения (ННБ).
По подсчётам аналитика компании «Дельта» Равиля Утяшева, среднегодовая потребность России во флотах (флот в нефтяной отрасли — совокупность различного оборудования для гидроразрыва пласта, ГРП) — 15 штук, насосах высокого давления — 48, роторно-управляемых системах — 150, катализаторах нефтепереработки для базовых процессов — 16,5–26,5 тысячи тонн, катализаторах нефтехимии — 15-18,5 тысячи тонн, системах каротажа — 90 штук.
До 2020 года российской нефтянке потребуется произвести сразу по 15 флотов и 90 систем каротажа (геофизического обследования скважин) ежегодно. Но пока лишь 10% оборудования для ГРП и 17% для ННБ изготавливают отечественные нефтесервисные компании ГК «Интегра» и консорциум «РФК».
В настоящее время свыше 300 российских компаний подключены к работе по замене зарубежных комплектующих на отечественные.
По оценке заместителя министра энергетики РФ Кирилла Молодцова, уже в 2017 году в ряде сегментов результаты этой деятельности станут заметны. Например, «Роснефть» запустила установку регенерации катализаторов на своём Новокуйбышевском НПЗ. Аналогичное оборудование непрерывной регенерации катализатора на установках короткоцикловой адсорбции смонтировано и на Туапсинском НПЗ компании. По подсчётам замминистра, замещение импортных катализаторов для нефтепереработки обойдётся российским производителям в 20 млрд рублей. Однако экономический эффект от замены этой технологии будет во много раз больше.
Большие планы по импортозамещению у АК «Транснефть». Например, для трассы трубопровода КТК (Каспийский трубопроводный консорциум, трубопровод проходит по территории ЮФО) планируется использовать систему контроля качества нефти, разработанную на великолукском «Транснефтемаше».
Оборудование для «Транснефти» изготавливают на волгодонском филиале компании «АЭМ-технологии» (основной актив — волгодонский завод «Атоммаш»). В недавней беседе с «Экспертом ЮГ» представитель компании рассказывал, что годовой объём продаж нового оборудования для нефтегазохимии (шиберные задвижки, колонное и реакторное оборудование, обратные клапаны) может превысить 500 млн рублей (заказчиками выступают «Газпром» и «Транснефть»).
Заказы от компаний нефтегазовой отрасли составляют 25% производимой продукции «Атоммаша», ранее продукция этого сегмента вообще не выпускалась в Волгодонске. Этот рынок в России крайне конкурентный за счёт большого количества игроков. Завод освоил производство новых продуктов: шиберных задвижек и обратных клапанов для магистральных нефтепроводов. Уже к 2015 году годовой объём продаж этих новых импортозамещающих продуктов превысил 500 млн рублей.
Гендиректор «АЭМ-технологии» Игорь Котов уточнил, что сегодня доля продукции для предприятий отечественной нефтянки у волгодонского и петрозаводского филиалов компании уже составляет треть из общего портфеля заказов. Благодаря загрузке заказами от компаний нефтегазодобывающего сектора выручка «АЭМ-технологии» выросла с 5,697 млрд рублей в 2013 году до 9,649 млрд рублей в 2016 году.
Оборудование на разрыв
В состав консорциума «РФК», специализирующегося на производстве мобильных комплексов ГРП, входит и ОАО «Тихорецкий машиностроительный завод имени Воровского» (ТМЗ). Именно это предприятие совместно с питерским ПКБ «Автоматика» и Минобрнауки РФ выступило с инициативой создания проекта первого отечественного мобильного комплекса на условиях частно-государственного партнёрства (стоимость проекта — 300 млн рублей). До этого все операции по ГРП проводились в России исключительно на импортном оборудовании. Как пояснили в Минобрнауки РФ, при сравнимых параметрах мощности и производительности российские технические решения обойдутся заказчикам на 20-40% дешевле, чем стандартные комплексы ГРП западного производства. К тому же сами мобильные установки будут работать на отечественном же газомоторном топливе.
Испытания тихорецкого комплекса ГРП производились на Кубани на действующих скважинах на Анастасиевско-Троицком месторождении ООО «РН-Краснодарнефтегаз» и на Патроновском газоконденсатном месторождении ООО «Газпром добыча Краснодар», показав прекрасные результаты. После чего РФК запустил их в серийное производство.
При этом в Ростове-на-Дону освоен выпуск оборудования для этой технологии, которое успешно применяется в ТЭКе. «Наша компания освоила выпуск установок нагрева технологических жидкостей (УНТЖ) мощностью от 1 до 3,5 мегаватт, используемых в процессе приготовления гелей при гидроразрыве пласта, — рассказал “Эксперту ЮГ” коммерческий директор ростовского ООО “Траст-Инжиниринг” Валерий Немыкин. — Их никто, кроме нас, не делает, а нефтегазовая отрасль теперь не зависит от зарубежных компаний».
«Таких компаний, как “Траст-Инжиниринг”, поставляющих оборудование для операторов, работающих по технологии ГРП, немного, — продолжает г-н Немыкин. — По технологии гидроразрыва в России сегодня работают “Газпром”, “Пурнефтеотдача”, “Татнефть”, ССК и другие. Отечественные компании давно занимаются импортозамещением. На сегодняшний день 70–80 процентов нефтесервисного оборудования уже производится в России, но далеко не всё можно заместить, и далеко не всегда удаётся добиться нужного качества».
Компрессорное оборудование для разработки ТрИЗов кубанской промышленной группы ТЕГАС успешно внедряют основные отечественные операторы. На Ковыктинском и Чаяндинском месторождениях (основа для будущего трубопровода «Сила Сибири») «Газпром» как раз использует мобильные азотные компрессорные установки ТЕГАСа.
Как пояснил в беседе с «Экспертом ЮГ» директор по производству компании «Краснодарский компрессорный завод» (входит в группу ТЕГАС) Валерий Татарин, ТЕГАС в течение 5 лет инвестирует 2 млрд рублей в проект по производству автоматических газонаполнительных компрессорных станций (АГНКС). Проектная мощность производства — более 300 в год.
«Роснефть» с помощью оборудования ТЕГАС намерена в ближайшие восемь лет ввести в эксплуатацию до тысячи автомобильных газонаполнительных компрессорных станций, став одним из ведущих игроков на отечественном рынке газомоторного топлива.
В поставках импортозамещающего оборудования для «нефтянки» на юге России отметились также Хадыженский и Каменский машиностроительные заводы, краснодарский «Нефтемаш», «Волгограднефтемаш», что позволило этим предприятиям увеличить чистую прибыль и выручку. Например, выручка «Нефтемаша» за последние два года увеличилась с 483 млн рублей до 600 млн рублей.
«Работа в сфере импортозамещения позволила “Волгограднефтемашу” увеличить выручку — с 5,6 по итогам 2015 года до 10,5 миллиарда рублей в 2016 году, — рассказал аналитик консалтинговой компании “Синан” Рубен Гаспарян. — Предприятие вышло в отечественные лидеры по производству реакторов, колонного, теплообменного и ёмкостного оборудования, работая с 27 крупнейшими нефтегазовыми компаниями России. Ранее это оборудование во многом закупалось в Европе».
Шельф меняет флаг
Предполагается, что тяжелее всего придётся разработчикам южнороссийского шельфа. В предыдущие годы работающие на нём ВИНКи отдавали заказы по нефтесервису, буровым работам, ГРР, поставкам глубоководного оборудования иностранцам. Но если ранее один «ЛУКойл» работал на каспийском шельфе, то в августе 2017 года ещё и «Роснефть» вышла на черноморский шельф в компании итальянской Eni, которой самой сложно будет сотрудничать в условиях санкций. Соответственно, теперь уже требуется куда больше оборудования и услуг для двух ВИНКов. Внутри России производится лишь 10% оборудования для этого (ёмкостное и часть насосно-компрессорного оборудования). А до 2030 года стране потребуется более 30 буровых платформ.
«В рамках госпрограммы “Развитие судостроения и техники для освоения шельфовых месторождений на 2013−2030 годы” на создание российских технологий для проектов на шельфе выделено 1,3 миллиарда рублей, — рассказал Кирилл Молодцов. — Эти деньги пошли на разработку бурового оборудования, средств морской разведки, донных сейсмических станций, комплектующих для судов обеспечения. В 2017 году будет начата работа по более чем 20 НИОКР по развитию судостроения».
Поддержка оффшорного судостроения дала толчок к возрождению целого пула судоверфей Астраханской области. Три года назад была создана Особая экономическая зона промышленно-производственного типа «Лотос» как центр производства комплектующих для судостроения, машиностроения и нефтегазовой отрасли. Место организации ОЭЗ такого профиля было выбрано не случайно: в регионе реализуются крупные нефтегазовые проекты, в том числе на шельфе Каспия, активно развито судостроение. Прост промышленного производства по итогам 2016 года составил 12 %, в судостроении – 15 %. В настоящее время в ОЭЗ "Лотос" пять резидентов, в том числе ведущий судостроительный завод Астраханской области "Лотос", который входит в Объединенную судостроительную корпорацию (ОСК). В ближайшее время статус резидента ОЭЗ "Лотос" получит еще одна компания - "Морское композитное судостроение" с проектом по производству композитных маломерных судов.
Только на ближайшие три года портфель заказов судоверфи «Лотос» превысил 5 млрд рублей. На верфи будут строиться химовозы, танкеры, нефтерудовозы и грузовые понтоны. Суда и оборудование для оффшорного бурения производятся также на местных верфях «Красные баррикады», АСПО, имени Карла Маркса и др., которые ещё несколько лет назад влачили жалкое существование и были на грани банкротства.
«Отечественные разработки стоят дешевле, а их качество зачастую намного выше импортных аналогов, — считает генеральный директор технологического холдинга “Петон” (свои НИИ в Уфе, Петербурге и Ростове-на-Дону), специализирующегося на нефтегазовом рынке, Игорь Мнушкин. — За счёт использования российских компонентов заметно упрощается логистика, сокращается время доставки оборудования. Более того, оборудование создаётся в соответствии с требованиями и нормами РФ, и нет нужды в дополнительных затратах на их адаптацию. Они полностью замещают зарубежные аналоги».