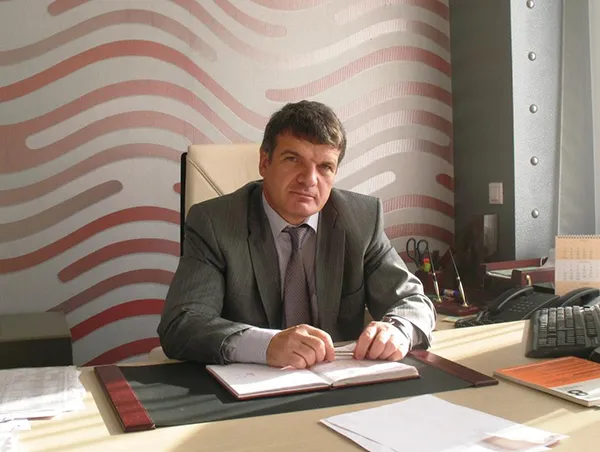
ООО «Полесье» образовано в 1998 году в Волгодонске (Ростовская область) как предприятие, специализирующееся на конструировании и изготовлении оборудования для энергетики, металлургии и нефтегазового комплекса. За 20 лет компания выполняла заказы на изготовление и поставку теплообменников, шлюзов для персонала, стеллажей для хранения топлива, ёмкостей и т. п. продукции для десятков заказчиков, наиболее крупные из которых — АЭС в России, Армении, Индии и Китае. Сюда же относятся такие крупные объекты атомной энергетики, как Ростовская, Калининская, Курская и Ленинградская АЭС, а также индийская АЭС «Куданкулам», китайская «Тяньвань» и «Руппур» в Бангладеш. Сегодня компания входит в единственный в России кластер атомного машиностроения (располагающийся тоже в Волгодонске), наряду с ещё 16 крупными, средними и мелкими предприятиями отрасли. В стратегии «Полесья» зафиксировано увеличение физических объёмов производства и выручки в горизонте двух-трёх лет. В компании считают, что добиться этого невозможно без создания новых условий для повышения производительности труда. С этой целью здесь рассчитывают на поддержку Регионального центра компетенций, созданного под началом Агентства инноваций Ростовской области, к сотрудничеству с которым приступили в этом году. Сейчас идёт работа по определению конкретных форм и направлений такого партнёрства.
В 2018 году «Полесье» перешло из сегмента малого бизнеса в средний: выручка составила около 1,4 млрд рублей против 785,8 млн рублей годом ранее. В ближайшие полтора-два года руководство компании намерено примкнуть к числу крупных компаний региона, перешагнув по выручке двухмиллиардный рубеж. Одна из причин динамичного роста — повышение производительности труда, внедрение принципов бережливого производства: такая работа здесь ведётся уже более 15 лет.
В интервью в рамках редакционного проекта «Бережливая индустрия Юга» учредитель и директор ООО «Полесье» Владимир Семенюк рассказал «Эксперту ЮГ», к каким результатам компания намерена прийти в ближайшей перспективе, что позволяет, а что мешает добиваться поставленных целей.
Настрой на перевыполнение плана
— Какова динамика производительности труда на предприятии за последние годы?
— За минувшие три года производительность труда на каждого сотрудника выросла с 70 процентов до 100 процентов. В ближайшие год-два должны довести этот показатель до 130 процентов. Сотрудники мотивированы на то, чтобы делать быстрее и больше. Те, кому это удаётся, получают премии. Сейчас премируются все сотрудники, в соответствии с достижениями. И знаете, перевыполнение каждым работником своего плана на 5–10 процентов стало для нашего завода типичным.
— Как в вашей компании делаются замеры производительности труда?
— У нас есть специальная программа, в которой зафиксированы нормы выработки (сколько времени надо на каждую производственную операцию, каким должен быть результат по итогам месяца и так далее), каждой операции присвоен индивидуальный штрих-код. Всё это заведено в единую информационную систему предприятия. После выполнения любой операции специалист отдела технического контроля (ОТК) по специальному штрих-коду определяет, выполнена операция или нет, насколько хорошо и быстро она выполнена. Для этого у нас есть специальные сканеры, как в супермаркете на кассе: подносят инженеры из ОТК аппарат к штрих-коду на экране монитора и тут же видна вся картина по выработке.
— Как вы оцениваете производительность труда на предприятии по сравнению с ситуацией в вашей отрасли в целом?
— В целом по отрасли сказать трудно. Думаю, мы все примерно на одном уровне находимся. Но у нас, как компании, выпускающей несерийную продукцию (отличающуюся по весу, габаритам, технологии, даже по видам сварки), есть своя специфика в отличие от тех предприятий, где действует конвейер, предполагающий выпуск одинаковых изделий в большом количестве. У нас всё-таки штучный товар, хотя и крупный: вес большинства изделий составляет десятки тонн.
— Оцените стадию, которую проходит ваша компания в процессе внедрения принципов бережливого производства.
— Идёт активное внедрение принципов бережливого производства. Это процесс постепенный, непрерывный и постоянный. Присматриваемся к лучшим российским и международным практикам, смотрим, что можно адаптировать к нашим условиям, и внедряем.
— Есть ли в вашей компании специальный программный документ для системы бережливого производства?
— Единого документа нет. На каждом производственном участке у нас действует приказ о повышении производительности труда. Наши рабочие выполняют свои плановые задания на производстве в соответствии с такими приказами. Эти приказы учитывают специфику каждого производственного участка.
— На какие структурные подразделения в компании возложено управление процессом внедрения бережливого производства?
— У нас нет отдельного структурного подразделения, этим занимающегося. Управление процессом бережливого производства осуществляют экономисты предприятия при моём личном контроле. Создание специального структурного подразделения по вопросам бережливого производства считаем нецелесообразным. И движущей силой, и контролёрами должны быть те, кто каждый день работает над повышением собственной производительности труда, то есть сами работники предприятия.
Я уже говорил, что у нас внедрена единая информационная система — программа «Каскад», которую разработал волгодонский предприниматель. «Каскадом» пользуются многие малые и средние предприятия кластера атомного машиностроения, в рамках которого работает и «Полесье». Эта компьютерная программа всё учитывает, в том числе и рост производительности. Итоги (сводная информация по каждому работнику) подводятся при помощи нажатия одной кнопки. Так что лишняя структура в управлении нам не нужна.
Жизнь стимулирует, бюрократия тормозит
— Что сегодня в наибольшей степени мотивирует вас заниматься бережливым производством?
— Это — жизненная необходимость любого предприятия. Без внедрения принципов бережливого производства сегодня невозможно повышать производительность труда. Без роста KPI каждого работника мы не сможем повышать людям зарплату, увеличивать их доход. И тогда они просто уйдут от нас к тем, кто больше платит. И если от нас уйдут квалифицированные кадры (которые и так в дефиците), мы просто разоримся. Мы работаем на рынке, где конкуренция не просто высокая, а довольно жёсткая, причём борьба идёт не только за каждого заказчика, но и за каждого перспективного работника. Сейчас в штате ООО «Полесье» 400 человек, и никого из них мы не хотим потерять. Наоборот, ещё могли бы принять 20–30 квалифицированных рабочих (сварщиков, станочников, слесарей). Только их негде взять: качество подготовки таких специалистов в специализированных колледжах и техникумах оставляет желать лучшего, талантливых ребят почти нет. Многие, обладающие квалификацией и опытом, хорошо устроены на других предприятиях Волгодонска, в том числе и по близкому нам профилю.
— Какие препятствия для внедрения бережливого производства вы считаете главными?
— Очень сильно мешает бюрократия в части подготовки различных документов. У нас, как компании-экспортёра, есть минимум четыре организации-контролёра (от нашего ОТК до представителей заказчика и государства, если речь идёт о поставках на экспорт). И для каждой из этих сторон надо готовить кипу бумаг, по каждому готовому изделию. Это — титанический труд, если учесть, что у каждого изготовленного на нашем производстве крупногабаритного изделия может быть до 100 контрольных точек (это, по сути, 100 этапов). Описание и заключение требуются по каждой из них. На взаимодействие с этими структурами уходят месяцы. Часто бывает так, что они между собой не могут договориться, прийти к единому мнению. Нам приходится ждать — продукцию без необходимых заключений и разрешений мы отправить заказчикам не можем. Происходит затоваривание наших мощностей. Работаем в две смены, и всё равно тесно, так как примерно треть наших площадей занимают цехи, остальное отдали под хранение материальных ценностей: комплектующих, материалов и, главное, готового к отправке оборудования. При более благополучной ситуации мы могли бы развивать производство (а не склад), ликвидировать вторую смену как менее производительную, работать в пять раз эффективнее, чем сейчас.
В приоритете — борьба с потерями
— Какие виды потерь наиболее актуальны для вашего предприятия и что вы намерены делать для их устранения?
— Длительный цикл изготовления продукции и огромные материальные запасы (сейчас на наших складах и в цехах комплектующих, материалов и продукции на сотни миллионов рублей). Ещё один вид потерь — вынужденные простои. При этом главные тормоза в развитии — первые два вида потерь. Простои — это лишь следствие. По мере устранения «складских завалов», сокращения цикла производства исчезнут и простои.
Как бороться с главными потерями? Совершенствовать технологию, оптимизировать процессы, в том числе и за счёт внедрения новых программных продуктов, инвестиций в развитие.
— У вас есть конкретный план инвестиций в бережливое производство?
— У нас есть комплексный план инвестиций в развитие производства, который находится на контроле у нашей службы качества. Ежегодно мы этот план актуализируем: анализируем, что и как выполнено; добавляем новые направления для инвестирования. Идёт работа по повышению качества продукции, технологическому совершенствованию производства, что, естественно, отражается и на повышении производительности труда, росте объёмов и выручки.
— Какой процент от выручки вы тратите на это?
— В среднем на инвестиционные мероприятия мы закладываем 10 процентов от выручки. Поскольку она растёт, то год от года это — разные суммы. Практически все средства направлены на развитие на нашей базе современного бережливого производства, по европейским меркам.
— Какие задачи в сфере внедрения бережливого производства компания ставит перед собой на ближайшие два года?
— Самая главная — увеличение производительности труда со 100 процентов до 130 процентов и выше. 20 процентов роста производительности мы сможем добиться за счёт снижения потерь, о которых я говорил, а ещё 10 процентов роста нам дадут различные технические мероприятия. Это, в частности, работа нашей инженерной службы, конструкторского отдела по усовершенствованию каждого рабочего места. Сейчас 70 процентов производственной площади у нас занимают материалы и готовая продукция, есть определённая стеснённость в цехах, особенно в сборочно-сварочных. Вот наши инженеры и решают, как сделать так, чтобы даже в этих непростых условиях люди могли работать с максимальным эффектом, экономя и жизненную энергию, и дефицитное время.
Понимаете, по западным меркам у нас низкая производительность труда. Есть такой показатель: товарный выпуск продукции в год на одного работника. У нас он составляет в среднем три-четыре миллиона рублей на человека, тогда как в ведущих западных странах (Германии, Японии, США) этот показатель вдвое выше (в пересчёте на рубли). Да, мы выполняем (и перевыполняем) собственные планы, возможные в нынешних объективных реалиях. Но цель-то у нас должна быть иной: семь-восемь миллионов рублей на одного работника в год вместо четырёх миллионов.
В нашей стратегии зафиксировано увеличение физических объёмов производства, выручки до двух миллиардов рублей в горизонте двух-трёх лет. А этого невозможно добиться без создания новых условий для повышения производительности труда. Здесь, на новом уровне развития бережливого производства, рассчитываем на поддержку Агентства инноваций Ростовской области, к сотрудничеству с которым приступили в этом году. Сейчас идёт работа по определению конкретных форм и направлений такого партнёрства.
— Вы говорили о том, что испытываете кадровый голод. Способно ли избавить от него более активное взаимодействие предприятия с вузами? Какие формы сотрудничества с ними, на ваш взгляд, наиболее перспективны?
— Возможны две формы. Первая — специальные учебные заведения и вузы готовят именно тех специалистов, которые компаниям нужны. По конкретным заявкам заводов, на высоком профессиональном уровне. Например, нам, как уже говорил, требуются квалифицированные сварщики и станочники, десятки специалистов. Вторая форма — преподаватели техникумов и вузов приходят на предприятие и читают лекции, например, по современным передовым методам металлообработки.
Однако, как показывает практика, подготовка профессиональных кадров в большинстве своём находится на очень низком уровне. И проблема не только в учениках, но и в преподавателях. Мы неоднократно убеждались в том, что они оторваны от производства и от реальной жизни, витают в каких-то теоретических эмпиреях. Именно поэтому мы передовые методы изучаем сами, в том числе посещая ведущие машиностроительные форумы в Москве и Ганновере (Германия), а кадры воспитываем, развивая на предприятии институт наставничества.