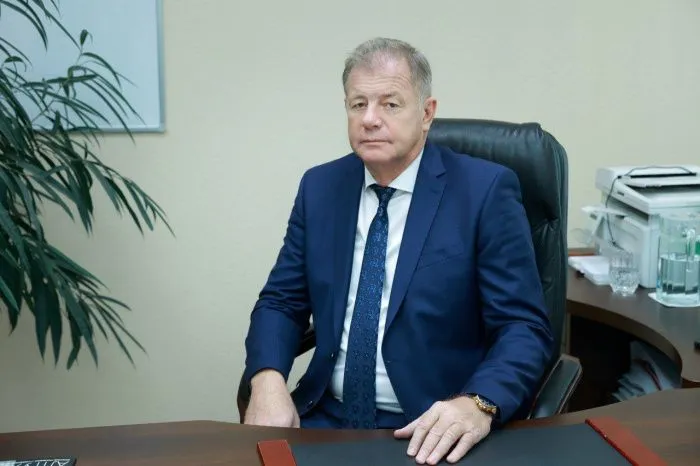
Юрий Павлович Коваль когда-то закончил военное училище в Краснодаре, затем — Академию госслужбы. 1990-е годы провёл в бизнесе, нулевые — на госслужбе: в южном полпредстве, Министерстве регионального развития. В 2010 году он занял пост вице-губернатора Волгоградской области по транспорту, позднее руководил технопарком «Мосгормаш» и ВНИИМЕТМАШ. А в 2016 году Коваль возвращается в Краснодар, чтобы начать возрождать завод, которым когда-то гордился край.
Беспрецедентный для промышленности случай
— На каком этапе находится инвестпроект, соглашение по которому вы подписали в 2023 году на форуме в Петербурге?
Мы построили новую площадку и запустили её в эксплуатацию. Это не отдельное предприятие, а одна из площадок, которая выполняет определённые производственные функции. В частности, там находятся термический цех, малярный цех, дополнительная обработка деталей. В целом мы за последние полтора года расширили свои производственные мощности практически в пять раз. Если у нас раньше были производственные площади в объёме 16 тысяч квадратных метров, то сегодня — 80 тысяч.
Российское станкостроение несколько отличается от китайского, корейского. Там широко используется кооперация. Вокруг станкостроительного завода, как правило, расположено много других предприятий, которые работают на этот завод. Одни льют базы, вторые производят отдельные комплектующие к станку. И конечный завод — это в большей степени сборочное производство. У нас же в России не так — потому что кооперация не так развита. В основном мы всё производим сами, в рамках одного предприятия — за исключением гидравлики, комплектующих для электрической части станка.
Для увеличения объёма производства нужно было, безусловно, увеличение производственных площадей и перевооружение. За последний год мы порядка двух миллиардов рублей вложили в техническое переоснащение, это только техническая часть. И, думаю, где-то полтора миллиарда составили инвестиции в стройку. Сейчас мы активно ведём реконструкцию площадей — в это тоже вложено порядка двух миллиардов. И вложения продолжаются.
Кроме того, мы планируем в следующем году начать строительство инжинирингового центра на территории завода. Это ещё порядка 25 тысяч квадратных метров. Сегодня мы активно ведём проектирование этого объекта, где-то во второй половине 2025 года выйдем в стройку.
— А что с выручкой предприятия? Там какая динамика?
— 2019 год мы завершили с объёмом выпуска 100 миллионов рублей. Этот год мы планируем завершить в объёме около 4 миллиардов. То есть за этот срок мы увеличили объём производства в 40 раз. На мой взгляд, для промышленности это беспрецедентный случай. В девятнадцатом году у нас работало порядка 120 человек, сегодня — 600 человек, при этом мы активно комплектуемся, нам как минимум нужно ещё 200. Тогда мы в год производили 10−12 единиц оборудования, сейчас — порядка 100. Мы начинали свой путь в рейтинге отрасли где-то на 30-й позиции. По итогам года мы войдём, как минимум, в тройку ведущих предприятий отрасли.
— Вы ещё видите потенциал кратного роста?
— Безусловно. Сейчас как раз идёт период подготовки плана финансово-хозяйственной деятельности на следующий год. В следующем году мы должны выйти на рубеж как минимум 6 миллиардов по выручке, что предполагает рост на 50 процентов. Отрасль сегодня растёт где-то на 15 процентов в год.
Как изменилась среда для станкостроения в России
— Основной спрос на вашу продукцию — внутри страны или за её пределами?
— В условиях санкций, конечно, это поставки только внутри страны. Хотя мы всё-таки созданы на базе завода им. Седина, были времена, когда он поставлял станки в 70 стран мира. Но это лидерство было потеряно, мы прошли непростые годы. Сейчас отрасль возрождается, принят федеральный проект по станкостроению. Наших производственных успехов не было бы без активной поддержки со стороны различных уровней власти.
Одной из ключевых форм поддержки являются льготные кредиты фондов развития промышленности — это и краевой фонд, и федеральный. Это также различные субсидии на НИОКРы. Мы много сегодня разрабатываем новых образцов продукции, новых видов станков, активно пользуемся мерами поддержки. Конечно, и различные возможности предоставления скидки для российских покупателей оборудования тоже позволяют делать нашу продукцию более конкурентоспособной.
— Кризис на ряде советских предприятий в постсоветский период случился из-за того, что исчез спрос на их продукцию. А у вас получается, что достаточно было заново начать её производить — и возникли такие темпы роста. В чём была главная проблема реформирования предприятия?
— Прежде всего, любая страна должна понимать, что основа промышленности — это станкостроение. Когда страна отказывается от собственного технологического суверенитета, это может закончиться очень негативно, что доказали события последних лет. Сегодня поставки в Российскую Федерацию практически любых станков из недружественных стран запрещены.
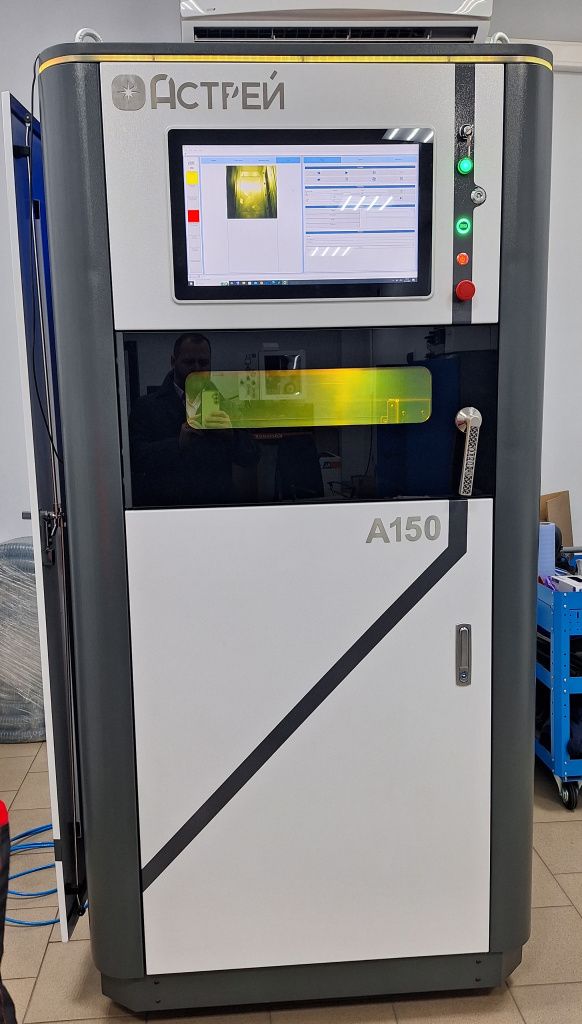
Когда рынок был наводнён импортным оборудованием, все деньги страны уходили туда. Закупая у них оборудование, мы фактически финансировали их дальнейшее техническое развитие. Нам тоже необходимы были средства на развитие, потому что станок — это высокотехнологичный продукт. Это когда-то в станках использовалась только механика, теперь ключевую роль играют системы управления, ЧПУ. Каждый день появляется что-то новое, а чтобы внедрять всё это, нужны приличные средства. Но получался замкнутый круг: раз у тебя нет заказчика и ты не продаёшь станок, то у тебя нет денег, ты не можешь развивать собственную науку, платить достойную зарплату инженеру и, в конечном счёте, создавать конкурентоспособный продукт.
Когда ситуация изменилась, когда мы поняли, что технический суверенитет должен иметь судьбоносное значение для страны, главные заказчики развернулись к своим производителям.
— Но вы же начали расти ещё до 2022 года. Я помню, что по итогам 2021-го у вас уже было за 400 миллионов выручки — в четыре раза больше, чем в 2019-м. Значит, развитие началось раньше — за счёт чего?
— Сначала мы перестроили стратегию предприятия и довольно приличные средства вложили в усовершенствование тех моделей, которые завод производил ранее. И эту продукцию заказчик оценил несколько по-другому.
Уже тогда наша власть начала делать первые шаги для поддержки станкостроения. Например, было введено дополнительное субсидирование покупки для российского потребителя.
За последние несколько лет мы разработали новые образцы оборудования, которое ранее не производилось. Сейчас наряду с линейкой, которую производил завод им. Седина, мы запустили ряд абсолютно нового оборудования, которое нами сконструировано, произведено и уже поставляется заказчикам.
На сегодняшний день мы производим фрезерные пятиосевые обрабатывающие центры, портальные обрабатывающие центры. Они запрещены к поставке даже в дружественных странах — в Китае, например. Мы за последнее время разработали, произвели и практически подготовили к серийному производству 3D-принтеры, позволяющие производить детали из металлических порошков. Сейчас мы завершаем разработку горизонтально-расточного станка, в России на сегодняшний день такое оборудование не производится.
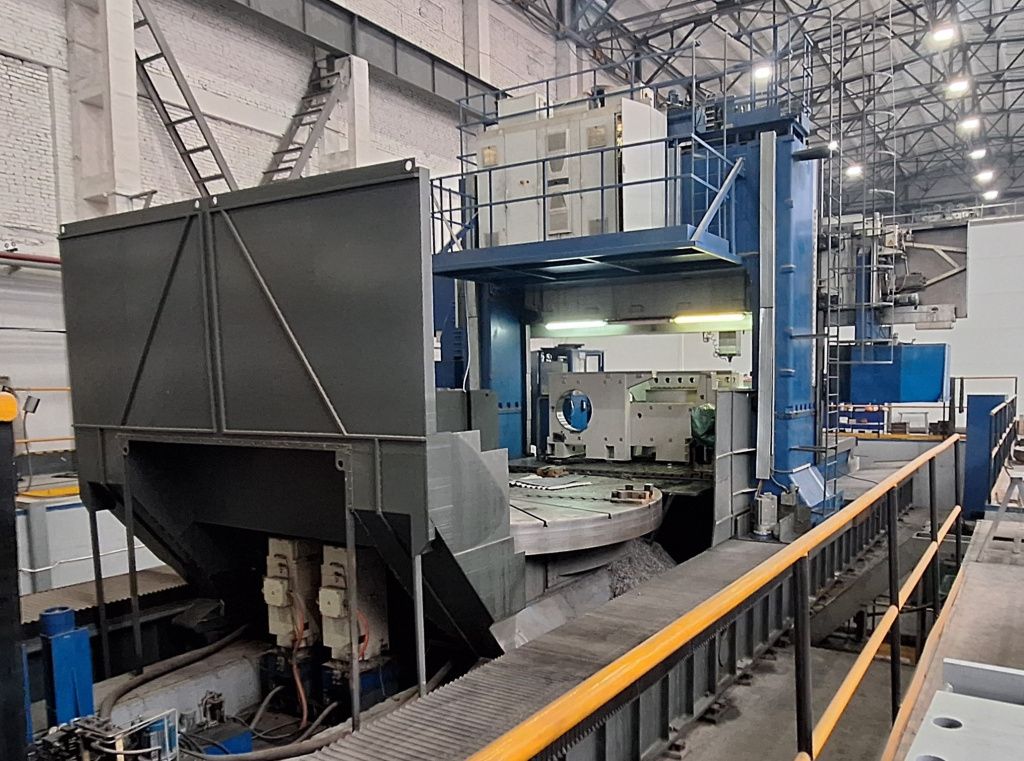
Кстати, нас часто сравнивают по ценам с китайскими производителями. Но сегодня я с полной уверенностью могу сказать, что дешевизна китайских станков — это миф. Недорогой китайский станок — это станок, на котором работать весьма проблематично. У меня из 20 станков, приобретённых в Китае, как минимум 5 стоят, потому что я уже полгода даже при помощи китайских партнёров не могу их запустить. Сегодня многие понимают, что карусельный станок завода им. Седина, произведённый 40 лет назад, гораздо надежнее, чем такой же станок, произведённый год назад в Китае. Сейчас нам проще общаться с нашими заказчиками, потому что прошёл определённый период, многие, купив недорогое китайское оборудование, поняли, что они не сэкономили.
— А можно выделить основные группы заказчиков?
— Прежде всего, скажу, что средняя стоимость нашего станка около 100 миллионов рублей — для малого бизнеса цена не совсем подъёмная. Нашими потребителями являются в основном предприятия оборонного комплекса, атомной промышленности, металлургические комбинаты, предприятия, связанные с космосом, крупные промышленные холдинги. Понятно, что это накладывает и на нас особую ответственность.
— А почему вы развиваете предприятие не в сторону кооперации, а как вертикально-интегрированную структуру?
— Я думаю, причин несколько. Вы помните советские времена, когда у предприятий было всё, начиная от пионерского лагеря, заканчивая собственным подсобным хозяйством, где на отходах столовой выращивали свиней. Это считалось правильным. Конечно, правда посередине: подсобные хозяйства промышленному предприятию ни к чему, но база отдыха для сотрудников, на мой взгляд, не помешает.
Во-вторых, у нас пока есть проблемы с надёжностью поставок в рамках кооперации. Сегодня даже разместить заказы в рамках кооперации сложно: не только у нас появилось много заказов. Предприятия, которые способны что-то производить, имеют огромный объём заказов. Далее, кооперация — это всегда спорный вопрос по цене, а это сказывается на себестоимости продукции. При этом любая кооперация — это, как правило, автоматом плюс логистика, а логистика — не очень дешёвое удовольствие, потому что у нас страна большая, мы не Бельгия.
А есть ещё проблема брака. Нас часто подводят и зарубежные коллеги — те же турки. Просрочки порой измеряются не неделями, а месяцами. Срыв условий выполнения заказов для оборонной промышленности грозит нам огромными проблемами. Поэтому мы сейчас планируем и своё литейное производство. Я думаю, что до середины следующего года его запустим. Но там, где кооперация возможна, мы её используем. Когда мы поняли, что технический суверенитет должен иметь судьбоносное значение для страны, главные заказчики развернулись к своим производителям
Как вырастить новое поколение конструкторов
— Но всё-таки разработка — это дело долгое, неконтролируемое по срокам. У вас под сукном лежали разработки или вы какие-то гениальные кадры собрали?
— Собрать можно только то, что есть. За последние несколько десятилетий плеяда конструкторов уже приблизилась к пенсионному возрасту — а новые не выросли. Последние 20 лет инженеры были не очень-то востребованы — все хотели стать юристами и экономистами. Мы взяли студентов второго курса три года назад, и под руководством нашего главного конструктора они начали расти. Прошло три года, из них уже 10 человек работают в штате как конструктора. Силами этих ребят, как ни удивительно, мы и создаём новые модели. Начинали эксперимент с Кубанским государственным технологическим университетом, сегодня работаем со многими вузами страны.

— А как вы их взяли? У нас же студент — вольная птица: хочу — иду, не хочу — не иду.
— Мы пришли на второй курс и говорим: «Ребята, кто хочет быть конструктором, а не курьером»? Набрали первые 20 человек, смогли их увлечь. Понимаете, что такое для молодого человека, когда делаешь не курсовую работу для того, чтобы отчитаться перед преподавателем, а конструируешь деталь реального станка? После того, как ты её нарисовал, ты спускаешься в сердце производства, идёшь к станочнику и говоришь, на что обратить внимание. После этого ты идёшь на сборку, берёшь свою деталь в руки и ставишь на станок. В итоге возникает такое чувство, которое вдохновляет.
При этом традиционно всегда были конструкторы, технологи, гидравлики. А мы сейчас пытаемся из них сделать инженеров. Потому что, когда человек проектирует станок, он должен понимать, как будет крутиться шестерёнка, как работает гидравлика, куда она подаёт жидкость, какая толщина трубки должна быть, чтобы создать нужное давление.
Традиционно процесс был устроен так. Есть конструктор — он сконструировал. Дальше технолог смотрит и запускает разработку в производство. Технолог посмотрел на конструкцию и спрашивает: «А как эту деталь сделать?» Конструктор ему отвечает: «Слушай, это не мое дело — я нарисовал, а ты думай, как изготовить». Здесь мы учим не так. Ты пойди в цех, посмотри, какое у нас есть оборудование. Если на нашем оборудовании это сделать невозможно, то эта конструкция нам не нужна.
— Это вы привнесли вот этот подход к обучению кадров?
— Ну конечно. Сегодня даже разнорабочих найти проблематично. И в этой сфере мы тоже пошли на один эксперимент, первыми в крае создали на предприятии УФИЦ (участок, функционирующий как исправительный центр. — «Эксперт Юг») при нашем ФСИНе. Сегодня у нас работает порядка 50 осуждённых. У них есть охрана, мы их привозим, увозим. По территории они передвигаются свободно, работают, как обычные люди. Как показывает практика, они проходят у нас социализацию — и очень многие остаются. Есть люди, которые в ходе отбывания наказания обучились, вышли на свободу и сейчас работают на самых сложных станках.
Органы не успевают за ростом организма
— Было много претендентов на территорию бывшего завода им. Седина, но в какой-то момент государство вмешалось. Что произошло после этого?
— Когда мы поняли, что первого помещения в 16 тысяч квадратных метров нам недостаточно, мы начали строить ещё одну площадку. Потому что были старые собственники завода, которые в 90-е годы приватизировали территорию, и нам не удалось найти с ними общий язык. Хотя мы предлагали выкупить предприятие. Позже оказалось, что приватизация была проведена с нарушениями. Суд принял решение — и вся площадка была возвращена в собственность Российской Федерации. Мы её на сегодняшний день выкупаем по частям. По этому поводу есть постановление правительства, обременение одно — площади должны использоваться для нужд станкостроения. Мы уже выкупили два ключевых производственных корпуса, один на 40 тысяч квадратных метров, второй ещё на 10 тысяч. А что ещё не выкупили — арендуем. Просто это довольно большие деньги. Плюс мы же выкупаем помещения в очень плохом состоянии — приводим их в порядок.
— Каков общий объём инвестиционной программы, например, за 2024 год?
— За последние три года объём инвестиций составил около 10 миллиардов. Я имею в виду выкуп площадей, строительство новых, приобретение нового оборудования, обустройство территории.
— А как бы вы сформулировали главный вызов, который стоит сейчас перед компанией?
— Это «детская болезнь» — болезнь роста. Когда кое-какие органы не успевают за ростом организма в целом. Понимаете, когда мы производили условно 10 станков, то комплектующие на них мог держать в голове начальник отдела снабжения. А когда их стало 100 разных, уже нет такого человека, который мог бы держать это в голове. И соответственно все службы должны перестроиться с 10 на 100. Это одна из самых сложных проблем. Мы сейчас запустили разработку и внедрение системы управления конкретно нашим предприятием. Очень недешёвая вещь. Я думаю, года три эта система будет внедряться. Она свяжет воедино все процессы, которые проходят на предприятии, и поможет эффективнее справляться с «детской болезнью».